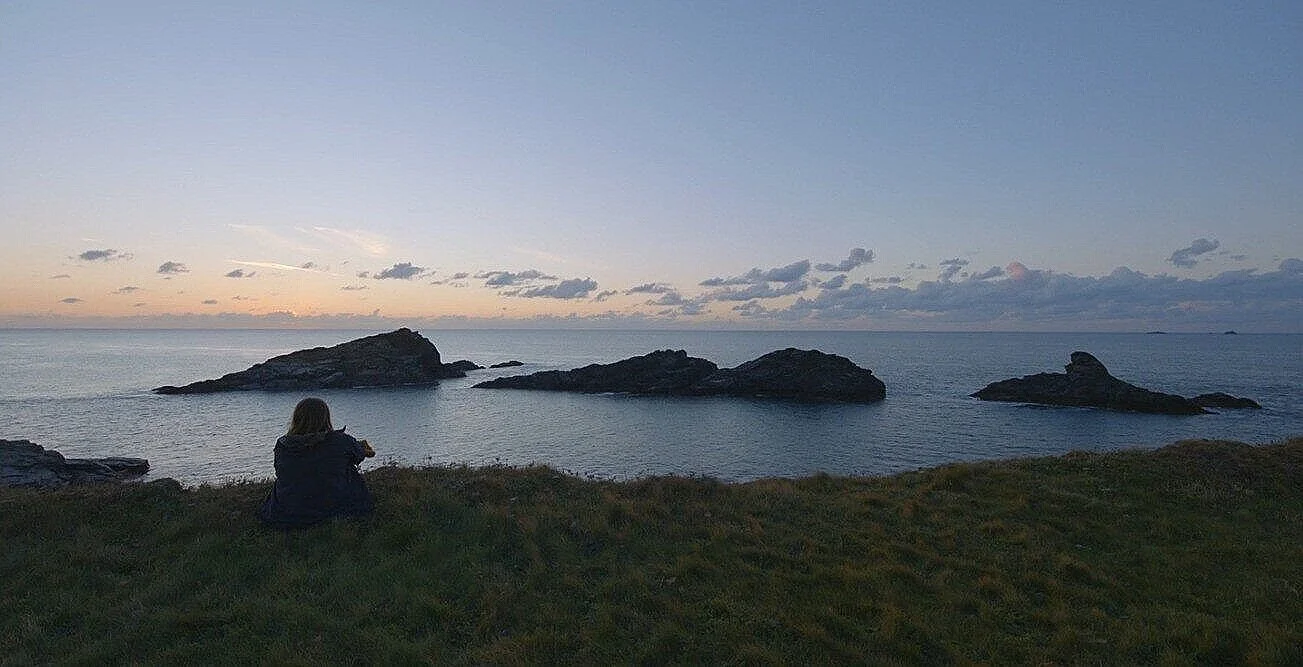
About
I am passionate about making work which connects me to the topography, flora and fauna of Cornwall. My playground has been the beaches, coast-paths and intertidal zones of the coast for decades. There is nothing better or nicer than meandering along the paths, walking across virgin sand left by the retreating tide or exploring the rockpools. It’s about bringing the outdoors indoors.
I work with glass powders and sheet glass to interpret my abstracted designs, building, layering and using multiple firings to create each unique Vessel. I sketch and draw, planning the designs but on the day the process is also organic and much of what I feel will influence the design further. Working in a semi structured way allows me to be organised but gives me the freedom to be responsive in the moment of making.
I love the freedom of the unknown, I love being able to react to an unexpected occurrence to develop the work as it is made. I am constantly learning and my work is an evolving process where each design feeds and informs the next. Its simple, I love what I do, it’s an adventure and a journey of discovery.
“The coastal colours, shapes and aesthetics are ever present in my vessel forms, allowing me to bring the outdoors indoors.”
Process
Forming the vessels involves several stages with multiple firings in the kiln, taking up to 24 hours for each firing. Utilising glass powders I layer, move, draw and compress it to form shapes and designs which are then fired in the kiln to fuse, resulting in glass wafers. Removing the wafer from the kiln the shape is refined by hand using diamond files and pads (cold working). The wafers are then layered onto sheet glass to be re-fired. On completion, the glass sheet is then suspended over a handmade mould with an aperture. Another firing ensues where I manipulate the temperature and time to control the glass descent through the aperture. Careful attention to this phase is crucial and carried out by numerous viewings by eye and unique to each vessel.
Next the excess glass is removed from the lip of the vessel, this leaves the vessel with sharp edges which need to be refined by cold working. The vessel may be finished at this stage or sandblasted and engraved to complete. Each unique and individual. I love each stage of the process.

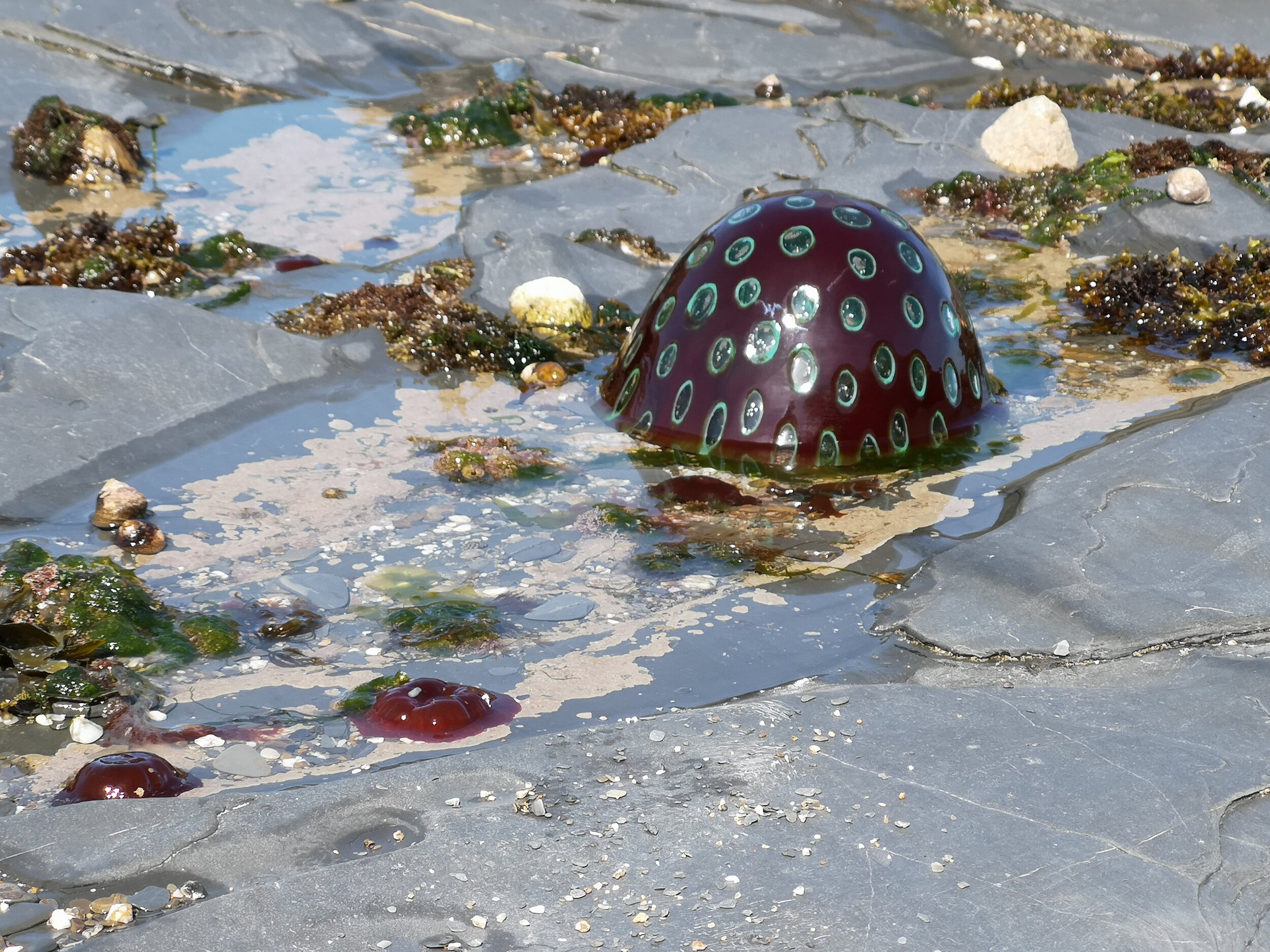
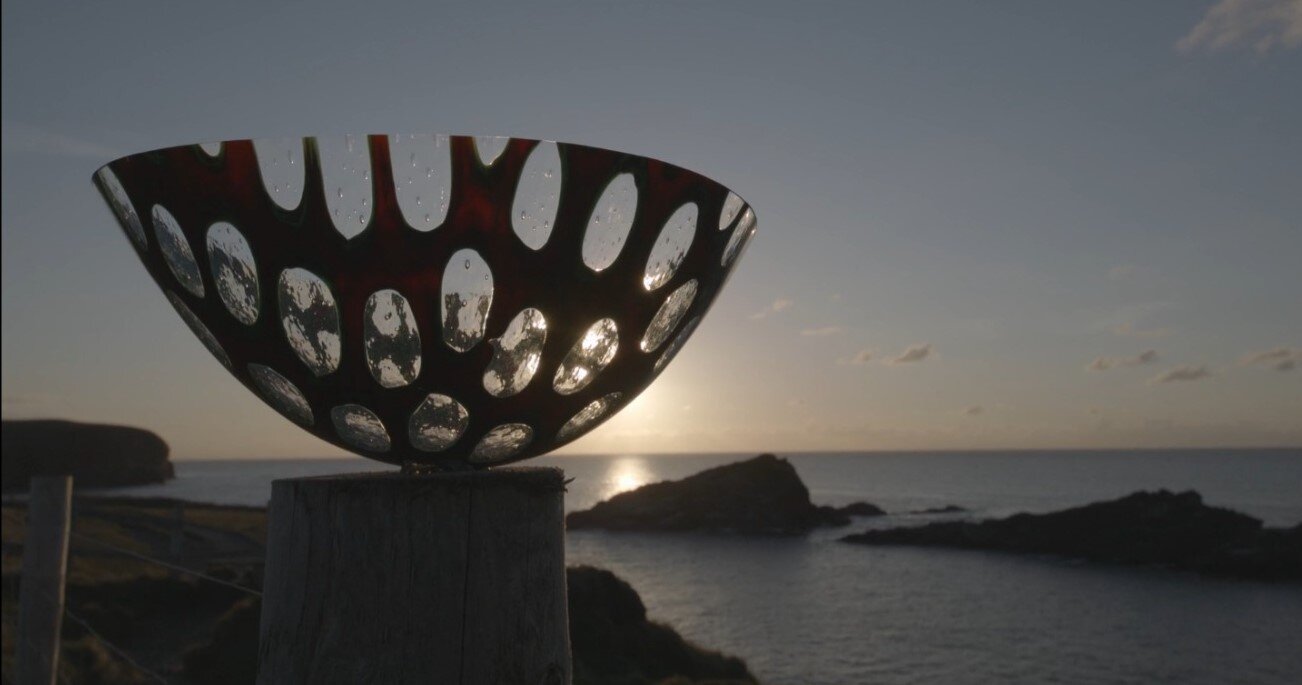
